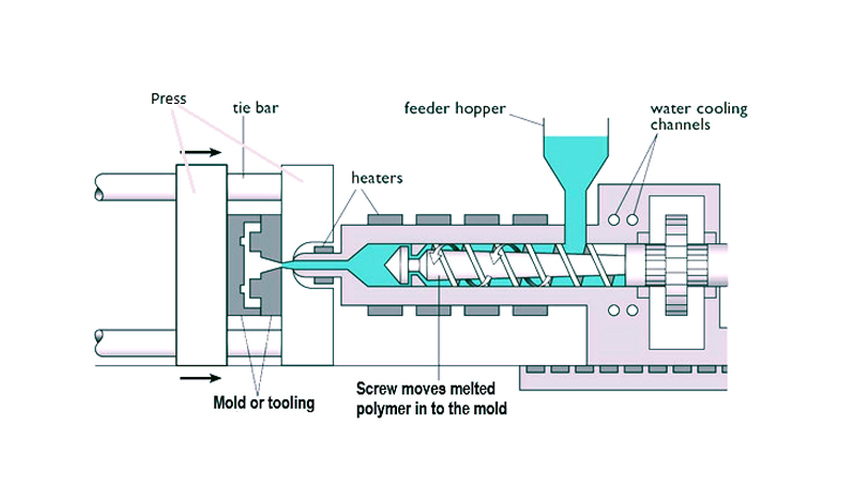
Injection molding started in the late 1860s with a product called celluloid (made of plant cellulose and camphor) used as a replacement for ivory in billiard balls. The heated celluloid was pushed through a plunger into a mold.
In 1912 Leo Baekeland made the first synthetic plastic, it had a phenol base he named it Bakelite.
Bakelite was heat resistant and non-conductive and highly moldable, so it was widely used as an insulator, as well as in many consumer goods.
As World War II wound down and consumer demand for inexpensive products grew the modern era of thermoplastics began.
Injection molding offered an inexpensive, repeatable process that could be used to create a wide range of consumer and industrial goods.
The simple plunger used for the celluloid billiard ball, has been replaced by using a heated screw and barrel so that temperatures and pressures of the melted polymer can be carefully controlled.
Now everywhere you look you will find items made of plastic, many of them, perhaps a majority, made with injection molding.
Injection molding is the most common way that 3 dimensional plastics items are made.
The following drawing shows how injection molded parts are created. The plastic injection molding machine consists of an extruder, a press and a mold or tooling.
Plastic Injection Molding Process for Creating Rigid Shaped Pieces
- The machine operator pours the polymer resin into the hopper.(The polymer arrives at the injection molding facility in pellet form, sometime polymer is already colored and other times there is a color concentrate added into the feed hopper)
- The hopper feeds the resin into the extruder.
- Heating elements and the turning of the extruder screw brings the polymer to the correct melting temperature and forces it through the extruder.
- Just before the shot of molten polymer flows in to the mold, the press brings the tooling into place with the correct clamping force necessary for the unique part being produced.
- As the tool and the molten polymer come together, there may be many moving pieces in the tool to assure that all the necessary spaces within the mold are filled.
- Once the tool is filled, the cooling of the mold begins in preparation for opening the tool. Immediately followed by the ejector pins pushing the parts off the mold. Then the process begins again.
- After the parts drop off the mold they may go through many more steps.
Injection molding is a remarkably cost effective process for many items we depend upon in our daily lives. These plastic injection molded items are found throughout our society:
- It may be the little cup filled with pre-measured coffee that you put in your one cup coffee maker.
- They may be part of an assembly in some complex medical application like a knee replacement.
- Or it could be an automobile dashboard that will go right to the assembly line and be snapped into place.
Contact us today to discuss your project requirements and discover how our expertise and capabilities can bring your vision to life. With TechNH as your partner, you can expect exceptional quality, precision, and reliability every step of the way.